2023年度水泥行业能耗数据介绍
发布时间: 2024/2/21 14:01:26
点击数量:
来源: 中国水泥网 韩彦峰
水泥行业是传统耗能大户,目前国内水泥企业用能还是以煤炭和电力为主,近二年水泥行业在能效方面取得了较大的进步,能效水平大幅度降低。最新版的《GB16780-2021水泥单位产品能源消耗限额》国家标准从2022年11月1日开始执行,2023年水泥行业实际用能情况如何?水泥行业能效水平到底在什么水平?下面简要介绍下2023年度国内水泥行业能耗数据情况。
一、水泥行业用煤情况
水泥企业主要是熟料烧成工序使用原煤,熟料单位产品综合煤耗指的是:在统计报告期内,用能单位生产水泥熟料消耗的煤、柴油等燃料量,折算成1 t水泥熟料消耗的标准煤量。
能耗限额一级是吨熟料标准煤耗94kg以下,目前约有6%以内水泥企业能达到,主要是新建生产线或者窑系统近二年进行了节能技改生产线,或者老线采用替代燃料,高热值危废等技术措施才能实现。
约25%以内的水泥企业吨熟料标准煤耗在在国标二级100kg以下。
约62%左右水泥企业吨熟料标准煤耗在二级到三级(109kg)之间。
剩余约7%以下的水泥生产线标准煤耗超过109kg,属于淘汰产能,或者需要技术改造。
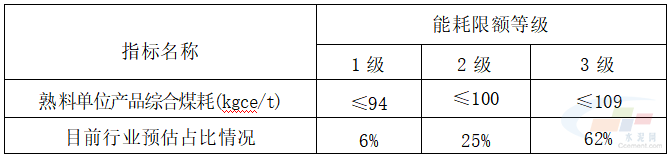
随着最近二年双碳政策的影响、行业技术的进步,加之市场竞争倒逼业进行内部挖潜,大型企业集团内部对标,相互竞争,新型隔热材料使用,预热器“五改六”节能改造、高效燃烧器、高效篦冷机的使用,节煤剂、替代燃料等节能措施的推广,2023年行业煤耗降低幅度较大,预估23年全行业平均的吨熟料标准煤耗约在100-103kg,并且呈现阶段性快速下降趋势。
标准煤是规定的7000大卡发热量的煤,实际并不存在这个煤,水泥厂实际使用的原煤发热量主流是5500大卡,100kg标准煤折算为127.3kg实物煤,103kg标准煤,折算为131kg实物煤。
如果一个标准5000吨熟料生产线,设计年生产熟料约155万吨,按照吨熟料实物煤耗127.3kg计算,年需要使用煤炭19.7万吨(绝大部分是烟煤)。但是目前水泥行业普遍超产20%,且实行错峰生产,全国各地区的熟料线实际产量差异很大,导致用煤量差异很大,需要具体分析。
23年的煤价每吨大概在800-1200元波动,均价约970元左右,吨熟料煤炭成本约970*0.1273=123.48元,如果按照970*0.131=127元,是熟料(水泥)成本中占比最大的单项成本。
2022年全国原煤消费量约48.49亿吨,2022年水泥行业煤炭消费量约2亿吨,占全国煤炭消费量的比例为4.05%,占比创9年新低。
二、水泥行业用电情况:
水泥行业用电粗略分为吨熟料用电量、吨水泥制备用电量二大块,有三个专业学术名词:熟料单位产品综合电耗、水泥制备工段电耗、水泥单位产品综合电耗
熟料单位产品综合电耗:在统计报告期内、用能单位生产熟料消耗的电能,折算成1t熟料消耗的电能。下图是目前各能耗等级占比情况。目前大部分水泥企业单位产量综合电耗在2级水平,目前超过61度电的熟料生产企业也不多,属于淘汰产能。
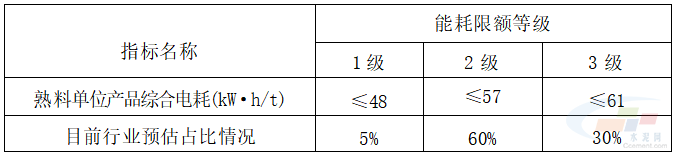
预估2023年全国熟料产品综合电耗平均值约56度电左右,并逐步下降。主要是这几年科技进步较快,加之市场倒倒逼业进行内部挖潜,大型企业集团内部对标,相互竞争,行业加大新型节能电机、水泵、空压机、变频器、预热器“五改六”节能改造等节能措施的推广,2023年行业电耗降低幅度较大。
同时国内熟料线基本都标配余热发电生产线,吨熟料发电量约在30度电左右,但是余热发电还需要自用2度电左右,实际净输出28度电左右。
水泥制备工段电耗:仅指从水泥熟料、石膏及混合材调配库底到水泥成品入水泥储存库消耗的电能,折算成1t水泥消耗的电能。下表是国标能耗限额等级和目前的行业实际情况。
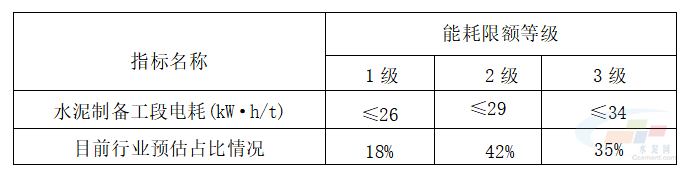
超过34度电的水泥生产企业也不多,多属于淘汰产能。
预估2023年全国水泥制备工段电耗均值约在28-29度电,并呈较快下降趋势,但是2024年6月1日水泥质量新国标执行后,水泥熟料系数会增加,水泥工序电耗会略微上升,24年行业水泥制备工段电耗均值会持平或者降幅减少。
水泥单位产品综合电耗:在统计报告期内,用能单位生产水泥消耗的电能,折算成1t水泥消耗的电能。统计范围内是从原燃料进入生产厂区到水泥产品出厂的主要生产过程和辅助生产过程消耗的各种能源,包含水泥生产用电,包装发运用电,混合材、石膏处理上料用电,加上辅助用电,再加上熟料单位产品综合电耗乘以熟料消耗总量计算的电量等合计总电量除以水泥产量。
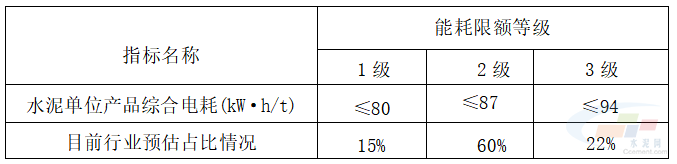
熟料生产还有附属设施用电,矿山开采破碎、输送用电,办公用电、检修用电等,吨熟料约5度电。水泥包装发运用电没有在水泥制备工段电耗统计范围内,吨水泥包装发运用电约5度电,吨散装发运用电较少不到1度电。
一条5000吨熟料生产线按照年产熟料155万吨,大概需要向电网购买的电量=155万吨*(56-28+5)=5115万度。
一个年产100万吨的水泥粉磨站大概需要向电网购买电量=100万吨*(28+2)=3000万度。
大部分省份实行分时电价,水泥行业熟料生产企业每度电均价约0.6元,粉磨站大部分采取夜间生产方式,综合电价要低于0.6元/度。
目前水泥过剩严重,生产线超产和错峰生产共存,加上部分熟料生产线还外卖熟料,具体到实际企业用电量需要根据真实生产熟料和水泥数量计算。
三、水泥行业用柴油情况
水泥企业用柴油量较少,主要是每次窑点火升温需要3-5吨柴油,每年每条线约点火2-10次,主要是北方近年来错峰生产较多,点火次数较多,每条线点火年使用柴油几十吨,总量较少(部分企业为了节省成本还使用燃料油代替);企业内和矿山叉车,铲车,挖机、运输车辆使用柴油相对较多,部分企业也选择外包模式,且目前政策要求逐步更换为新能源车辆,整体来说水泥行业直接使用柴油数量较少,间接物料运输车辆使用柴油数量较多。
四、熟料单位产品综合能耗、水泥单位产品综合能耗(kgce/t)
这二个指标也是水泥常见能耗指标,比如工信部能效领跑者就按照熟料单位产品综合能耗排名申报。
熟料单位产品综合能耗指的是在统计报告期内,用能单位生产水泥熟料消耗的各种能源,折算成1t水泥熟料消耗的能源量,包括用煤、柴油、用电量×0.1229计算出来的。
水泥单位产品综合能耗指的是在统计报告期内,用能单位生产水泥消耗的各种能源,折算成1t水泥消耗的能源量,是熟料单位产品综合煤耗×熟料系数+水泥单位产品综合电耗×0.1229+水泥生产烘干热耗(大部分企业没有)计算出来的。
0.1229为国家规定的常用系数,每千瓦时电力折算标准煤系数,单位为千克标准煤每千瓦时。
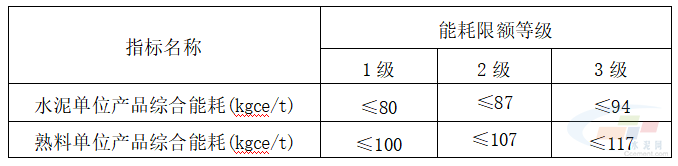
五、其他能源使用情况
目前国内水泥行业使用重油和石油焦等燃料的较少,国外较多使用重油燃料,特别是沙特地区,大部分使用重油,部分地区使用石油焦,全球水泥行业使用天然气的也比较少。目前水泥行业使用替代燃料的越来越多,特别是近二年随着煤价上涨,水泥价格下跌,各大水泥企业为了降低生产成本,加大了替代燃料的使用,国内华新水泥在替代燃料方面做的最好(2023年度国内熟料生产线TSR超过20%)。氢(氨)能在水泥行业已经开始进行实验,距离真正商业化应用还有很长的路要走。在绿电方面,目前国内越多越多的水泥企业建设光伏发电和储能电站,随着光伏发电和储能成本近期大幅度降低,水泥行业自建绿电的会越来越多,自建绿电产能越来越大。
六、综述
2023年水泥行业整体能源消耗量还是比较大的,主要是因为水泥产量基数大,但是受双碳政策的影响,行业的技术进步,加之市场竞争,销售价格下滑倒逼业进行内部挖潜,大型企业集团内部对标,相互竞争,以及新型隔热材料使用,高效燃烧器、高效篦冷机、节能电机、风机、空压机等节能设备的使用,节煤剂、替代燃料的使用,预热器“五改六”节能改造等节能措施的推广,加之落后高耗能企业的退出,水泥行业能效水平在大幅度的下降,全行业肯定能达到国家发改委2022年2月发布的《高耗能行业重点领域节能降碳改造升级实施指南(2022年版)》中要求的“到2025年,水泥行业能效标杆水平以上熟料产能比例达30%,能效基准水平以下熟料产能基本清零”的既定目标,甚至部分指标会超越要求,在全体水泥行业人员的共同努力下,水泥行业整体节能降碳效果显著,绿色低碳发展能力大幅增强。
此文章来源于中国水泥网信息中心,如有侵权请联系作者删除。